トンネル掘削の現場を劇的に変えた、 日本初の技術。
1990年当時、トンネル掘削で出た土砂は、ダンプカーなどによって坑外へと搬出されるのが常識でした。 この工法に一石を投じたのが、タグチ工業の「延びるベルトコンベヤ」です。 日本では誰も手掛けていなかった新しいチャレンジ。 タグチの〈連続ベルトコンベヤシステム〉の登場は、日本のトンネル工事を大きく変えることとなりました。
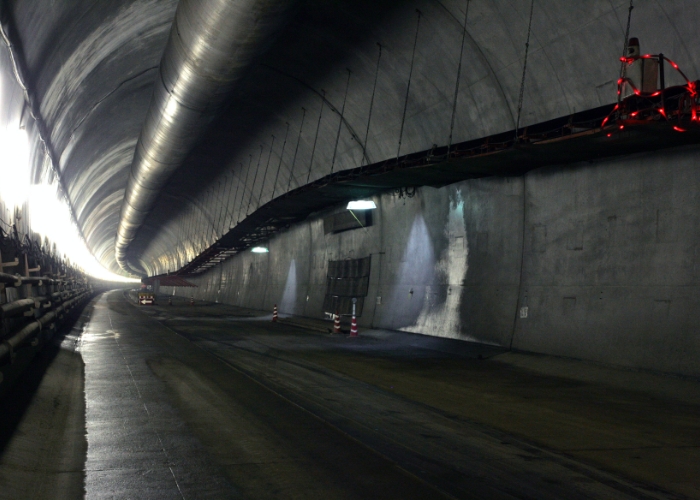
効率、コスト、安全、そしてクリーン… 導入のメリットをご確認いただいた初納入
タグチ工業が開発を続けてきたNATM用〈連続ベルトコンベヤシステム〉が、97年5月、九州新幹線田上トンネル工事で採用されました。まずは、ホコリが立ち視界も悪い中を、土砂をいっぱいに積んだダンプトラックが行き来することを、当たり前だと考えていた作業スタッフが、坑内のクリーンな環境に驚きました。作業効率の点をみても、コストの点からみても、〈連続ベルトコンベヤシステム〉採用のメリットは、大きなものでした。この成功があったからこそ、その後着実に、全国の現場へと広がっていったのです。
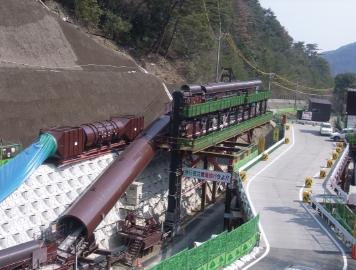
▲二段式のストレージカセットを採用し、設置スペースを小さくした事例(石榑トンネル)
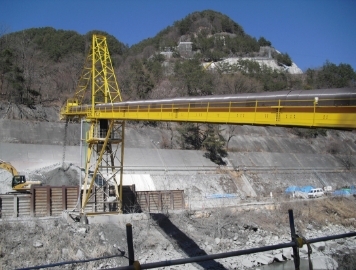
▲抗口の前を流れる川を挟み、対岸まで土砂を搬出した事例(小渋トンネル)
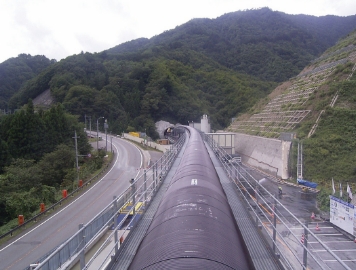
▲坑口から300mのコンベヤで土砂を一気に搬出した事例(栗子トンネル)
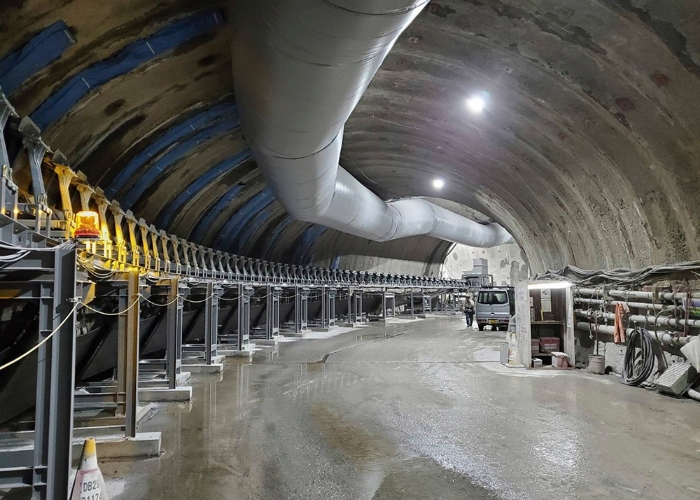
都市土木の分野からも注目を集める、 曲がるベルトコンベヤ
パイプコンベヤのようにベルト部を完全に丸めず、十分な搬送量を確保しながら、急カーブへの対応を可能としました。ベルトの速度は、毎分90〜150m。土砂の搬出能力は1時間あたり約300tを実現しています。最小の曲線半径は30m。60mの幅があれば、180度のターンも可能です。この柔軟性が、効率化と安全性を追求する、今後の都市土木のニーズにもしっかりとお応えしていきます。

課題から学びとり、また次の課題へ
東京の地下40mを、9.1km掘り進む「東京外かく環状道路・本線トンネル東名北工事」。地上では住宅が密集し、車が激しく行き交うこの環境のなかに〈連続ベルトコンベヤシステム〉を導入したいというご要望を受けて、当社の技術者が開発したのが、縦型のストレージカセットでした。他にも、このプロジェクトによってタグチ工業は、新たなノウハウを得ることができました。これからも進む都市地下空間の有効活用で、必ずやお役に立てるものと信じています。
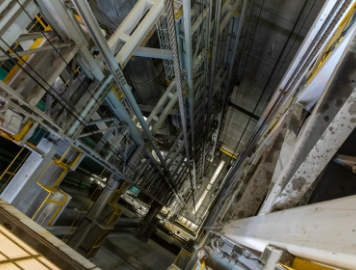
▲掘削が続けられているのは地下40m。この縦の空間にリフトを設置しました(東京外かく環状道路)

▲切り羽までの最長距離は9.1km。当社の〈連続ベルトコンベヤシステム〉がどこまでも追随します(東京外かく環状道路)

▲土砂の搬出能力は1500 t/h。安心のシステムが、休むことなく働き続けます(東京外かく環状道路)
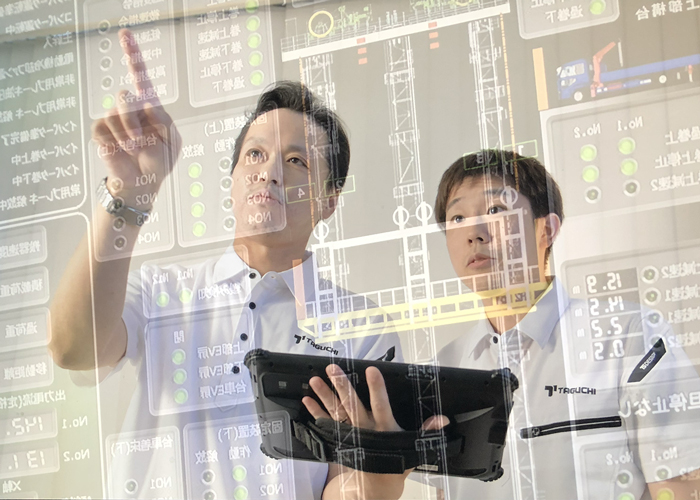
安全稼働を見守り続ける監視システム
現場の作業効率に大きな影響を及ぼす、当社の連続ベルトコンベヤシステム。常に良好な稼働状態を保ち、万一トラブルが発生した際にも早急に復旧できるよう、リアルタイム設備監視システム〈ベルコン・マネージャー〉による万全の監視体制が整えられています。全国で稼働中の連続ベルトコンベヤシステムを見守るのは、福岡本社と東京支店に設置されたオペレーションルーム。この2つの拠点で、当社の技術者が稼働状態をリアルタイムで監視しながら、トラブルの予兆はないかを見守っています。このシステムにはPLC(プログラマブル・ロジック・コントローラ)が使用されていますので、オペレーションルームからの遠隔操作も可能です。技術者が現場に駆けつけるタイムラグをなくし、稼働率を最大限にまで高めるために導入されたタグチ工業の新たなチャレンジに、どうぞご期待ください。
*閲覧にはWEBブラウザを使用していますので、PC、タブレット、スマートフォンなどからいつでも現状をご確認いただけます。
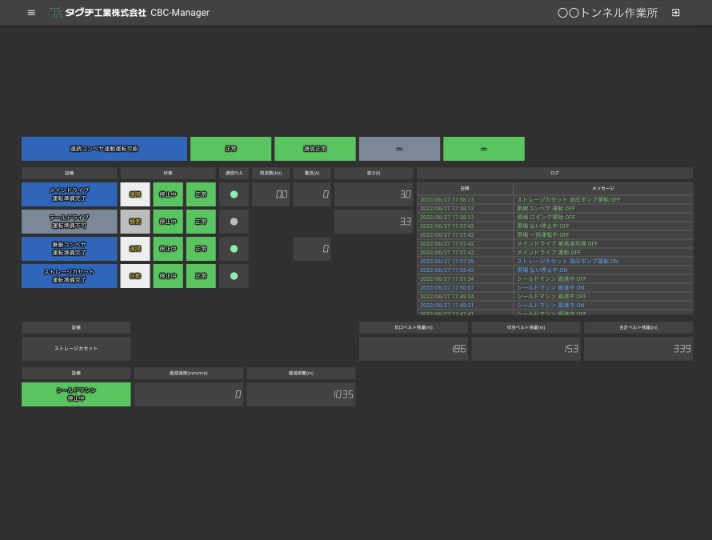
▲リアルタイム監視画面。各現場で稼働するメインドライブ、テールドライブ、ストレージカセットなどの状況を表示します。
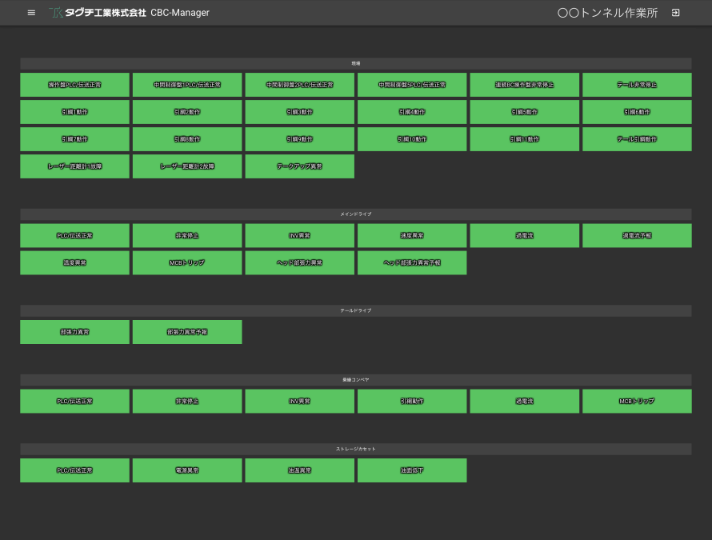
▲アラーム詳細画面。トラブルの際には、故障箇所を一覧で表示。いち早い復旧を支援します。(画面は正常運転の状態)
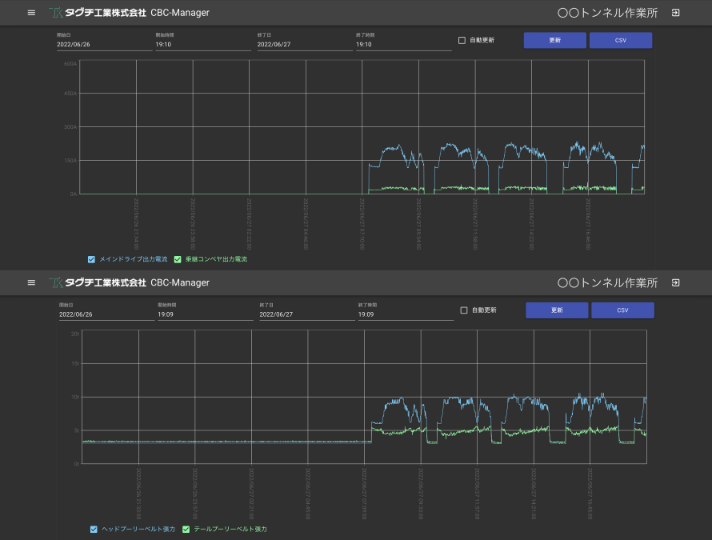
▲電流値(上)とベルト張力(下)のトレンドグラフ。電流値の変化からは、ずり質の変化も確認・予測できます。
効率的で、環境にやさしい現場を実現するために 再び脚光を浴びる「タグチの斜行技術」
高低差のある現場に、人員、資材、車両を、安定して安全に運搬するために、 1989年、日本初の工事用インクライン設備として万場ダムで実証された、タグチ工業の斜行技術。 工事全般の効率化を図るとともに、 長い現場へのアプローチ用道路を必要としないインクライン設備は、 二酸化炭素の排出量や森林伐採面積の削減にも貢献します。 これらの相乗効果によってタグチの斜行技術は、いま再び脚光を浴び始めています。
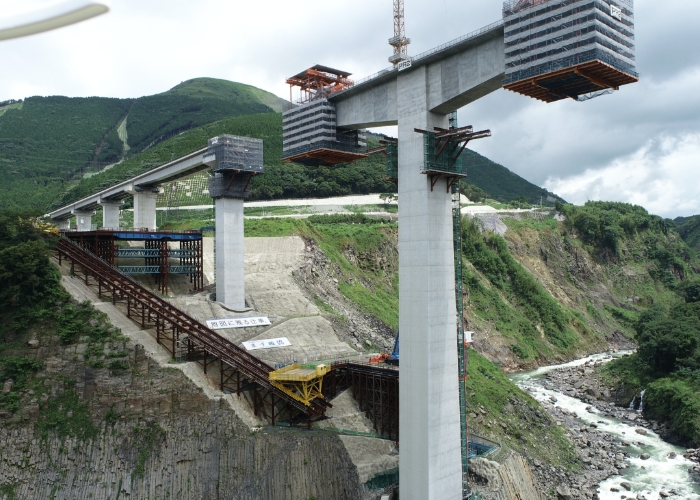
標準的な工期を約1年半短縮 効率性と安定性に、全国の現場が注目
熊本地震で落橋した阿蘇大橋の架替事業として架設された「新阿蘇大橋」。近隣の人々は、1日でも早い完成を期待していました。その工期を短縮するための手段のひとつとして採用されたのが、タグチ工業のインクライン設備です。必要とされる現場まで、大量の資材や車両を安定して運搬するインクライン設備の活躍によって、標準的な工期を1年4ヶ月短縮することに貢献しました。この実績に対する土木業界からの評価は高く、新阿蘇大橋工事の成功を受けて、当社のインクライン設備の導入は、全国の現場へと広がっていきました。
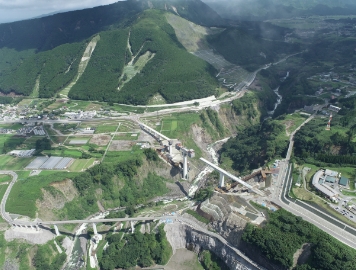
▲2016年4月の熊本地震により旧阿蘇大橋が崩落。一日も早い復旧は、地域住民にとっての念願でした(新阿蘇大橋工事)

▲急峻な峡谷の難工事でしたが、標準工期に比べて1年4カ月短縮しての早期供用を実現しました(新阿蘇大橋工事)

▲2021年3月7日、熊本復興のシンボルとでもいうべき新阿蘇大橋が開通しました(新阿蘇大橋工事)
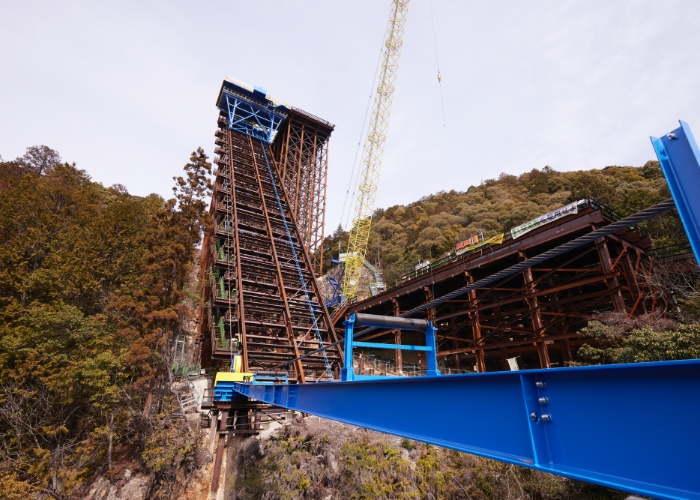
高低差63.2mを3分46秒で… 高い次元の安心と安全を実現
新名神高速道路の中で、最も高い橋脚が必要となる「信楽川橋工事」。すぐ近くにまで山肌が迫り、インクラインの設置には、課題の多い環境でした。勾配の角度は54.25度。これは様々な現場にインクライン設備を納入してきたタグチ工業でも、はじめて経験する急角度です。この勾配を安全にスムーズに走行させるために、私たちが選んだのは500kwという大出力の巻上機。ワイヤーロープの直径も60mmとなっています。このゆとりを持たせた設計のおかげで、63.2mの高低差を、3分46秒という安定したスピードで結んでいます。
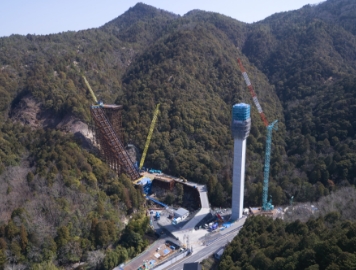
▲もっとも高い橋脚は97m。その作業を行う上部構台まで、工事用資材や車両を運びます(信楽川橋東工事)
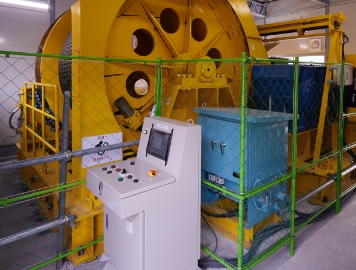
▲巻上機の出力は500kw。これまで使用してきたものの中でも、最大の出力を誇っています(信楽川橋東工事)
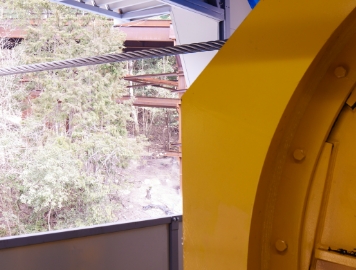
▲直径60mmのワイヤーロープが、台車をスムーズに引き上げています(信楽川橋東工事)
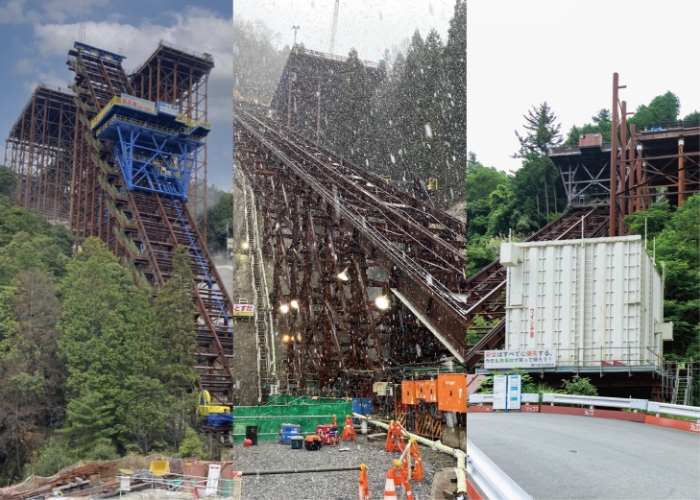
幅広い分野への応用が期待される ベーシック&シンプルな斜行技術
工事の着工にあわせて稼働できるよう現場に設置し、工事終了とともに解体・改修する。タグチ工業のインクラインは、これまで仮設設備として、全国の現場に導入されてきました。そして今、当社の斜行技術の安定性や効率性にご注目いただいたお取引先から、常設設備としてのインクラインに対するオファーが増えています。たとえば、ダム湖の清掃に欠かせない除塵機を、湖面の上下に合わせて調整する設備の技術開発にも、現在着手しています。日本初の技術を開発し、今日まで継承し続けてきたベーシックでシンプルなタグチ工業の斜行技術。今後ますます、その応用範囲は広がっていきます。
高低差のある現場をダイレクトに結ぶ、 100tクラスの大型リフトも得意分野のひとつ。
山岳土木の分野では、現場へのアプローチに高低差がある場合が多くあります。 そのような現場へと、資材や車両を最短距離で運ぶのが、 様々な現場で活躍している、タグチ工業のリフト設備です。 すでに完成された技術と言われるこの分野にも、タグチ工業は新しいアイデアと技術を導入。 業界の常識を再び覆そうとしています。
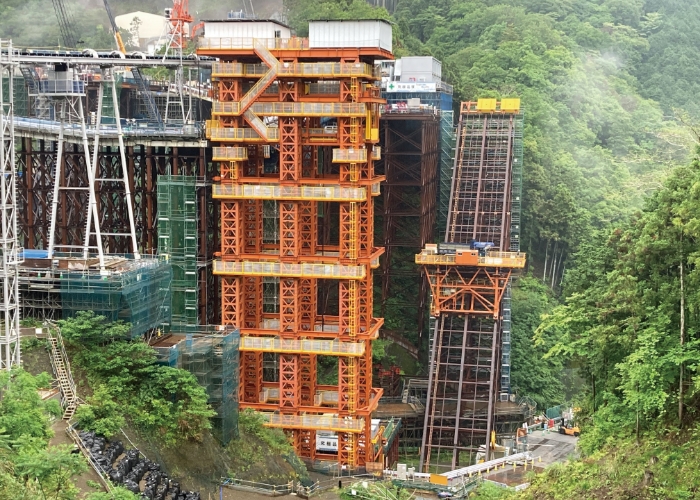
全国各地の現場での安定した運用実績に、ますます高まる信頼性
特に高低差の激しい山岳土木の分野では、工事用資材や車両の、現場へのスムーズな搬送が、工期に大きな影響を及ぼします。どのような環境下でもスムーズな運行を続けるタグチ工業のリフト設備に安定感は、全国の様々な現場で実証されています。納期の短縮やコストの削減など、日々寄せられるお客様からのご要望に応えるため、綱に新しい発想で、問題解決にチャレンジを続けています。
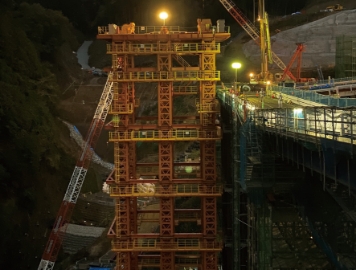
▲最大積載荷重46tの大型リフトが、建築資材や車両を現場へと送り届けます(新東名高速道路 山北皆瀬川工事)
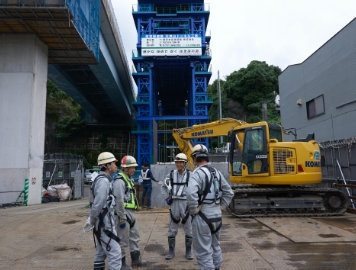
▲高低差15mの現場まで、安定した速度で搬送します(佐世保道路 天神山トンネル工事)
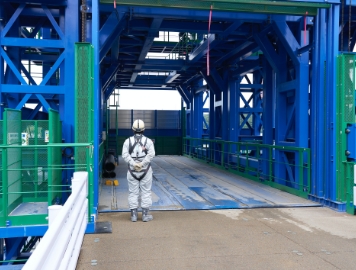
▲最大積載荷重46t。荷物を満載した10tトラックを、2台同時に運びます(佐世保道路 天神山トンネル工事)
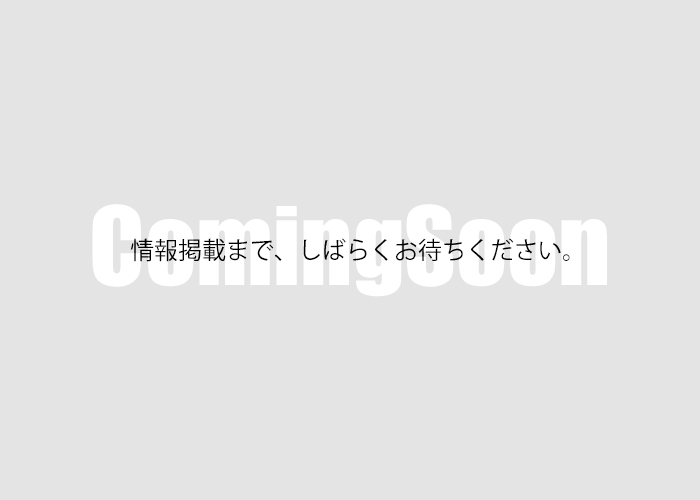
当社技術者の、柔軟な発想から生まれた 新工法に集まる、業界の注目!
シールド工法の資材搬入に不可欠な立坑。その内部を上下するリフト設備としてもタグチ工業の製品は採用されています。1日の工期短縮が数千万円のコスタダウンに寄与すると言われるシールド工法では、リフトの設置期間の短縮も、お客様からの切実なご要望のひとつでした。そこで当社の技術者が考案したのが、これまでリフトを支えてきた4本の支柱を、ロックコイルに変更するという画期的なアイデアでした。この新発想によって、リフトの設置は、従来の1/3にまで短縮することができました。新しい工法のスタンダードになるか否か、土木業界は今、この新技術を静かに見守っています。
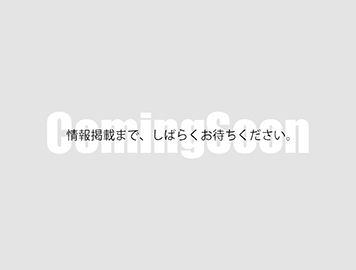
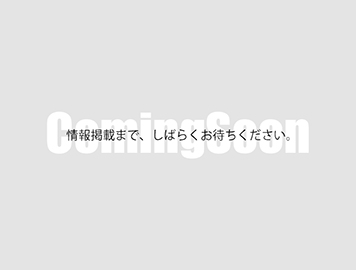
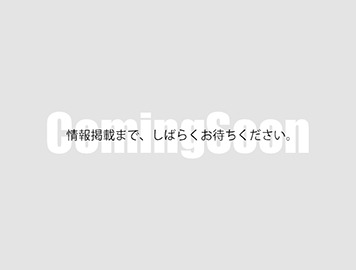
タグチ工業の母体となる技術への、 誇りを胸に、脈々と未来へと継承。
そもそも、タグチ工業のスタートは立坑設備から。 当社の草創期である1950年代から設計技術者をドイツ、カナダ、アメリカなど欧米諸国へ 派遣し技術を磨いてきただけに、この分野では大きな信頼を集めてきました。 LPガスの安定供給を目的に、国家レベルでプロジェクトがすすめられている 「水封式地下岩盤貯蓄方式」のLPガス国家備蓄基地工事にも当社の立坑設備が採用されています。 近い将来、必ずや必要となるこの技術を着実に未来へと継承していくために、 タグチ工業は環境を育み、人を育て続けています。
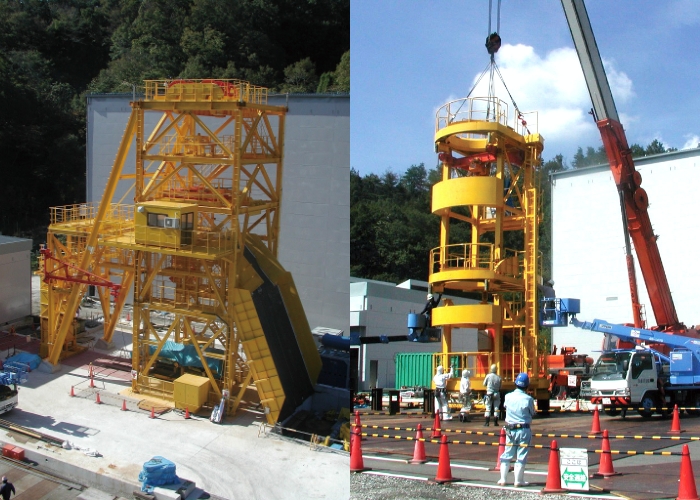
▲瑞浪超深地層研究所 研究坑道掘削工事に採用された立坑設備
放射性廃棄物処分技術の研究にも 貢献するタグチの立坑技術
原子力発電のサイクルの中で発生する高レベル放射性廃棄物。その処理には300mよりも深い地層で、長期間にわたる保管・管理が必要となります。その研究のため計画されたのが、超深地層における処分技術の研究坑道です。地下500mの立坑を掘削し、地中の岩石や地下水などを調査するこのプロジェクトに、タグチ工業の立坑設備が採用されました。現在では当社のみが、日本国内で唯一、立坑技術を継承し続けています。放射能廃棄物処理の計画が、研究段階から実施段階へと進んでいく今後、当社への期待は、ますます大きなものとなっています。