The first technology in Japan that dramatically changed tunnel excavation sites.
In 1990, dump trucks were commonly used to remove sediment from tunnel construction. Taguchi Industry’s expanding conveyor shook up this custom. It was a challenge no one had taken on in Japan. The introduction of Taguchi’s continuous belt conveyor system significantly changed Japanese tunnel construction.
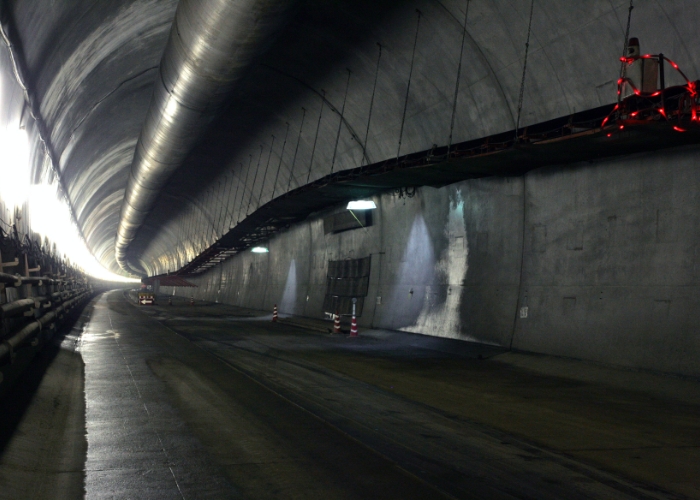
This first delivery confirmed the benefits of the installation: efficiency, cost, safety, and cleanliness
The NATM continuous belt conveyor system developed by Taguchi Industry was adopted in the construction of Kyushu Shinkansen Tagami Tunnel in May 1997.The construction staff were initially surprised by the clean shaft environment because they had taken for granted the passage of dump trucks loaded with lots of sediment in a space with poor visibility, swirling with dust.The benefits of using a continuous belt conveyor system were significant from the perspectives of both work efficiency and cost.Thanks to this success, the system spread steadily thereafter to sites throughout Japan.
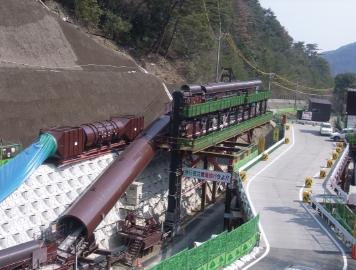
▲A bilevel storage cassette is used to reduce the size of the installation space (Ishigure Tunnel)
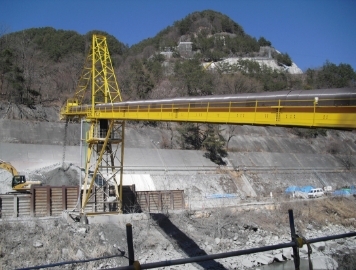
▲Transporting sediment across the river that flows in front of a shaft entrance to the opposite side of the river (Koshibu Tunnel)
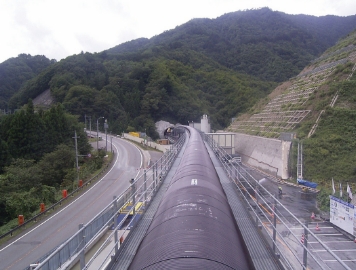
▲Transporting sediment by a 300 m conveyor from a shaft entrance all at once (Kuriko Tunnel)
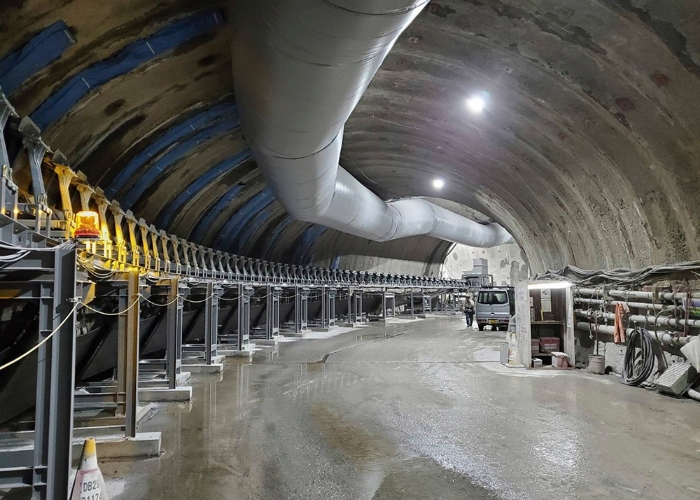
Curved belt conveyors also gaining attention in the field of city engineering
The belt section is not completely rounded off like a pipe conveyor, allowing it to handle sharp curves while ensuring sufficient transporting capacity. Belt speed is from 90 to 150 m per minute, achieving a sediment-transporting capacity of around 300 t per hour.The smallest curve radius is 30 m.With a width of 60 m, even a 180-degree turn is possible.This flexibility will also answer fully to future city engineering needs in the pursuit of efficiency and safety.

Gathering knowledge from present challenges to face the next
Construction of the Tokyo Outer Ring Road Main Line Tunnel of the Tomei Expwy. burrows 9.1 km, 40 m beneath Tokyo.We received a request for a continuous belt conveyor system in this environment, where aboveground housing clusters and cars pass incessantly, and our engineers developed a vertical storage cassette. Thanks to this project, Taguchi Industry also gained other new expertise.We are confident that our technology will be helpful for the effective use of underground spaces in cities, which will be increasingly in demand in the future.
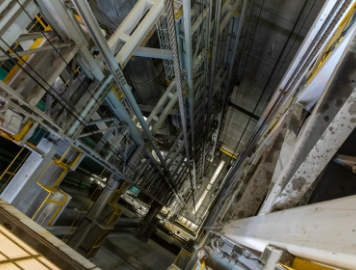
▲Excavation continues 40 m underground.We installed an aerial work platform in this vertical space. (Tokyo Outer Ring Road)

▲A total distance to the face is 9.1 km. Our continuous belt conveyor systems meet requirements anywhere. (Tokyo Outer Ring Road)

▲Sediment-transporting capacity is 1500 t/h.Our secure systems continue working without rest. (Tokyo Outer Ring Road)
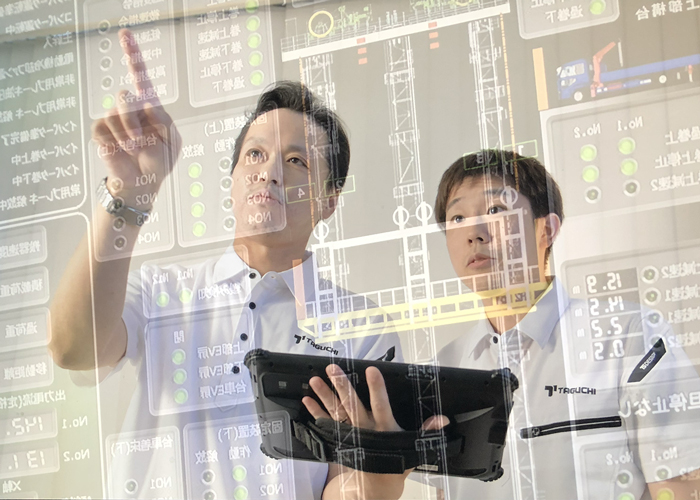
A surveillance system that continues to protect secure operation
Our continuous belt conveyor system has a significant impact on onsite work efficiency.The belt conveyor is monitored perfectly thanks to the Belcon-Manager real-time equipment-monitoring system, which constantly maintains good operating conditions and allows prompt restoration even in the event of trouble. Operation rooms installed at the Fukuoka Head Office and Tokyo Office oversee all continuous belt conveyor systems in operation around Japan. From these two locations, our engineers monitor operating conditions in real time and stay on guard against signs of trouble. This system uses a PLC (programmable logic controller), which allows it to be operated remotely from the operation rooms.Taguchi Industry introduced the system to eliminate delay caused by engineers rushing to sites and maximally improve operational efficiency. We hope you will look forward to the new challenges we take on.
*Viewing is available via web browser, so current status can be checked using a computer, tablet, or smartphone.
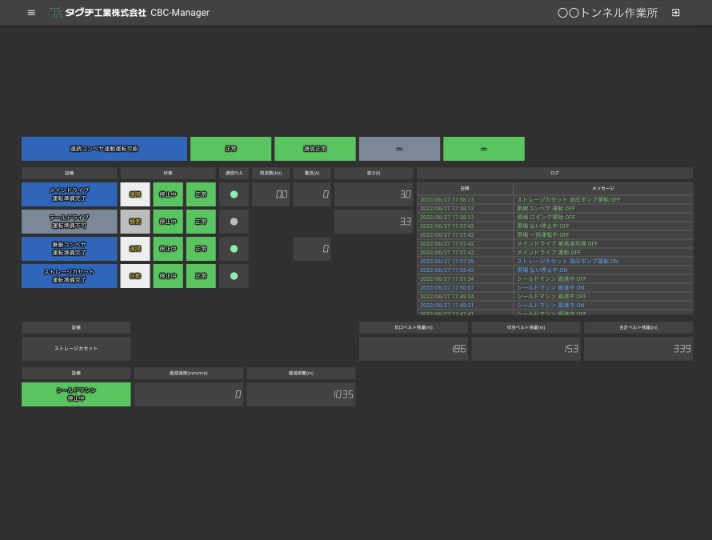
▲A real-time monitoring screen.It displays the status of the main drive, tail drive, and storage cassette at each site.
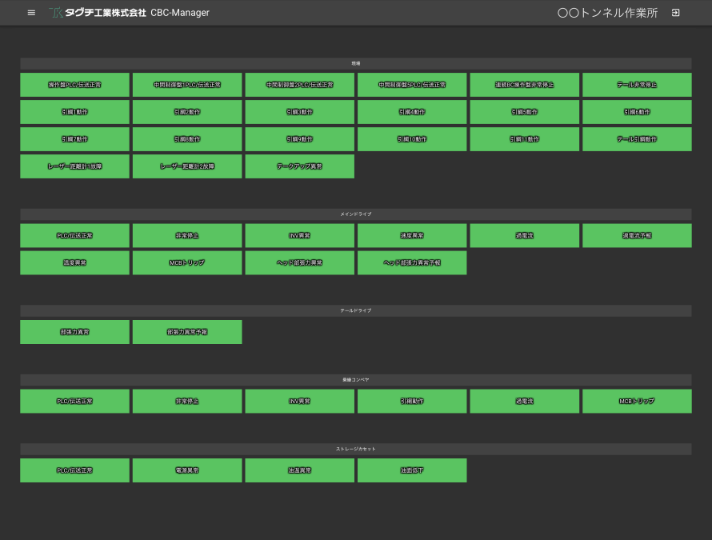
▲An alarm close-up screen.When trouble occurs, a list of defective parts is displayed to support quick restoration.(The screen shows normal operation status.)
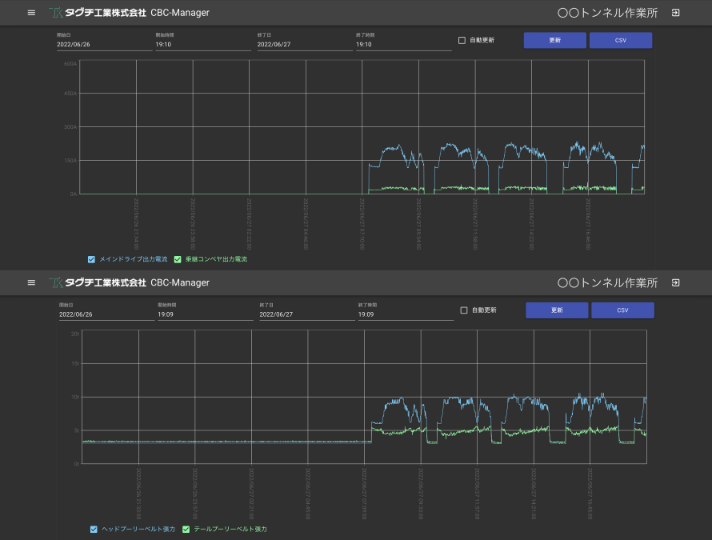
▲Trend graphs showing current value (above) and belt tension (below).Changes in debris quality can also be confirmed and predicted from changes in current value.
Taguchi’s inclination technology is once more in the limelight for achieving efficient, eco-friendly sites.
Taguchi Industry’s inclination technology proved itself at Banba Dam in 1989 as Japan’s first inclined construction equipment for securely, safely transporting people, materials, and vehicles to sites with differences in elevation. In addition to making construction more efficient overall, inclined equipment that does not require a long approach road to the site contributes to reducing carbon dioxide emissions and deforestation area. Thanks to this synergy, Taguchi’s inclination technology is once again in the limelight.
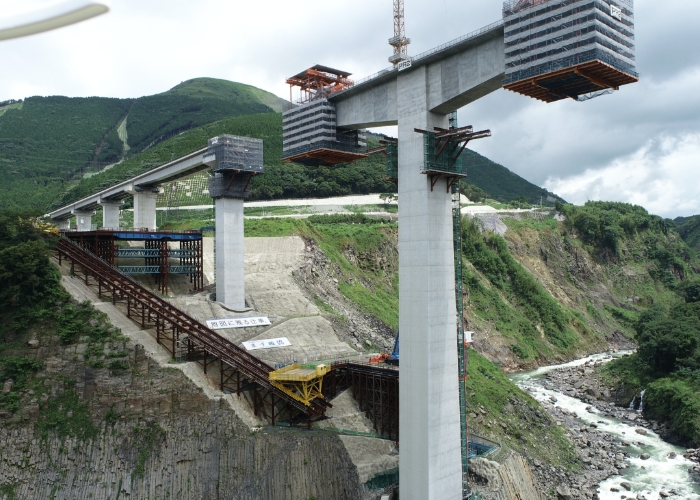
Average construction time shortened by about a year and a half, attracting attention from sites across the country for its efficiency and stability
The Shin-Aso Bridge was built to replace the Aso Bridge, which collapsed in the Kumamoto Earthquake.Locals hoped for the fastest possible completion. Taguchi Industry’s inclined equipment was used as one means of shortening construction time.Successful use of the inclined equipment to transport a large amount of materials and vehicles safely to the site contributed to shortening the average construction time by one year and four months. Introduction of our inclined equipment spread to sites throughout Japan due to the high rating of these results by the engineering industry and the success of the Shin-Aso Bridge construction.
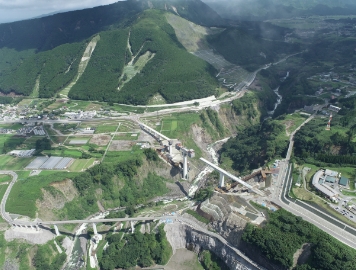
▲The old Aso Bridge collapsed in the Kumamoto Earthquake of April 2016. The greatest wish of local residents was for its fastest possible restoration. (Shin-Aso Br.)

▲It was difficult construction work in a deep canyon, but the bridge became useable early thanks to a construction period shortened by one year and four months compared with the average. (Shin-Aso Br.)

▲The Shin-Aso Bridge, a symbol of Kumamoto’s recovery, opened on March 7, 2021. (Shin-Aso Br.)
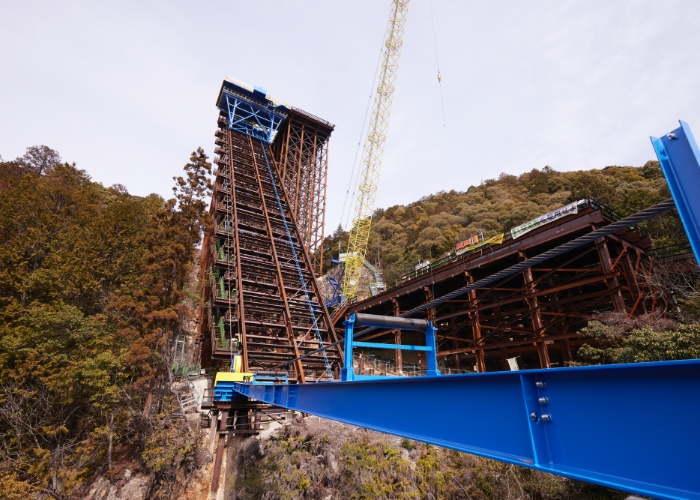
Connecting the 63.2 m elevation difference in three minutes and 46 seconds, our inclines provide a high level of security and safety
Construction of the Shigarakigawa Bridge required the highest bridge pier on the Shin-Meishin Expwy.With the mountain’s surface pressing near, the environment posed many challenges for inclined equipment. The slope angled at 54.25-degree.Even for Taguchi Industry, which had delivered inclined equipment to a variety of sites, this was the first experience with such a steep angle.In order to travel safely and smoothly on this slope, we chose a 600 kW high-output winding machine.The diameter of the wire rope is also 60 mm. By securing the design leeway, a difference in elevation of 63.2 m is connected at a stable speed in three minutes and 46 seconds.
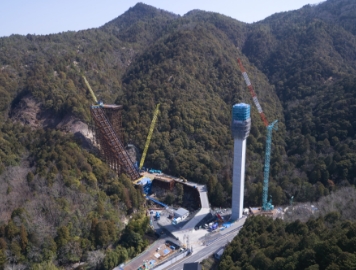
▲The highest bridge pier is 97 m.Construction materials and vehicles are carried to the upper platform where the work is to be performed. (Shigarakigawa Br.)
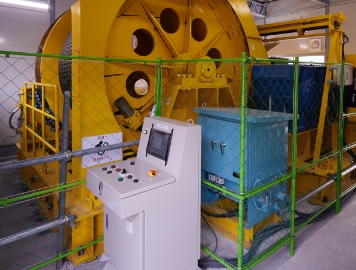
▲The output of the winding machine is 600 kW: the maximum output of anything previously used. (Shigarakigawa Br.)
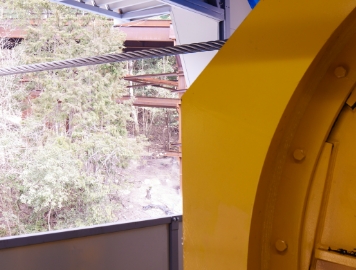
▲The 60 mm-diameter wire rope smoothly aerial work platforms the cart. (Shigarakigawa Br.)
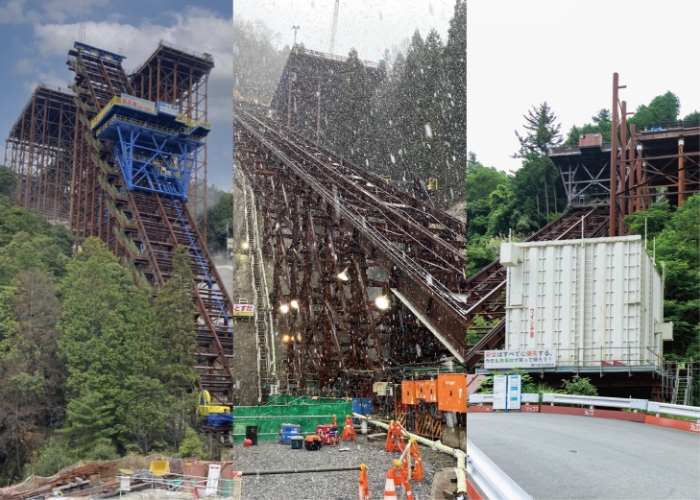
Basic and simple inclination technology with potential for wide range of fields
Installed at sites to operate as soon as construction starts, then disassembled and repaired when construction finishes.Taguchi Industry’s inclines were previously introduced at sites throughout Japan as temporary equipment. Now, offers for permanent equipment are increasing from customers who have taken notice of the security and efficiency of our inclination technology. For example, we have currently begun technological development of equipment that adjusts the dust extractors essential in reservoir cleaning according to the rise and fall of the water surface.Taguchi Industry’s basic, simple inclination technology was developed as the first in Japan and has continued to this day. The range of its applications will continue to expand even more in the future.
We also specialize in large 100 t capacity aerial work platforms that directly connect sites with differences in elevation.
In the field of mountain engineering, there are many cases of elevation differences in the approach to sites. Taguchi Industry’s aerial work platform equipment transports materials and vehicles to those sites by the shortest distance. Taguchi Industry introduces new ideas and technology even in this field that is already considered to be perfected. We are attempting to once more shake up common practice in the industry.
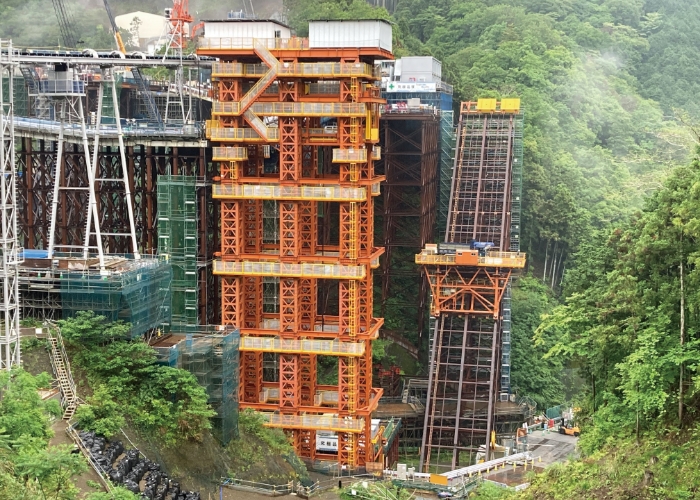
Increased reliability with stable operational results at sites throughout Japan
Particularly in the field of mountain engineering, with extreme differences in elevation, smooth transport of construction materials and vehicles to sites has a significant impact on construction time.The sense of stability Taguchi Industry’s aerial work platform equipment gives by continuing smooth operation in any type of environment has been proven at various sites around Japan. We continue to challenge ourselves to solve problems, always with new ideas, to respond to daily requests from customers for things like shortened delivery time and cost reduction.
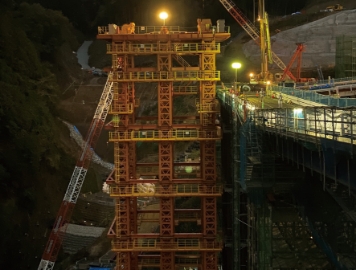
▲Our large aerial work platform with a 46 t maximum load delivers construction materials and vehicles to the site. (Shin-Tomei Expwy. Yamakita Minasegawa)
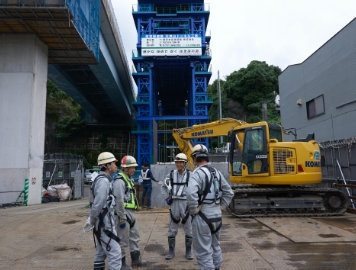
▲Transportation to the site with a 15 m difference in elevation at a stable speed. (Sasebo Road Tenjinyama Tunnel)
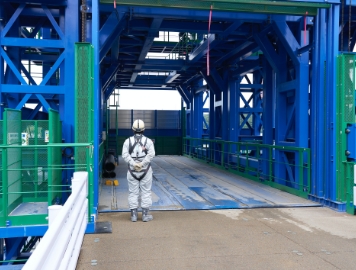
▲A maximum load of 46 t. Two fully-loaded 10 t trucks are transported at the same time. (Sasebo Road Tenjinyama Tunnel)
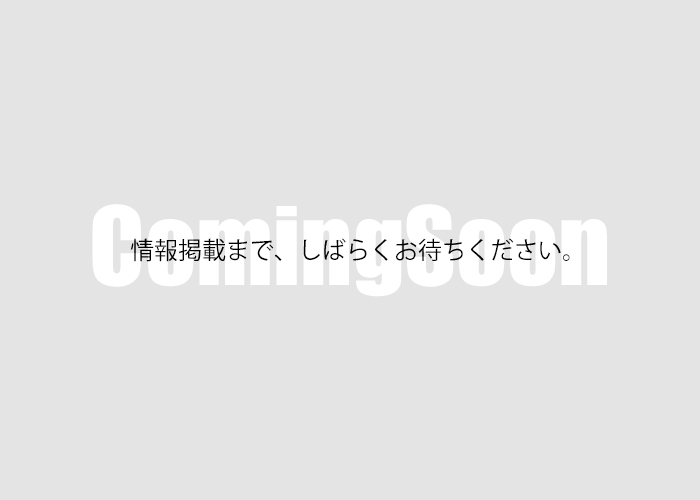
The new construction method, born from our engineers’ flexible thinking, gains attention in the industry!
Shafts are indispensable for transporting materials in the shield method.Taguchi Industry’s products are also used as aerial work platform equipment that raises and lowers in those shafts. In shield construction, even shortening the construction period by one day contributes to reducing cost by tens of thousands of yen; therefore, shortening the aerial work platform installation period was also an urgent customer demand.Accordingly, our engineers came up with the revolutionary idea of replacing the four supports that previously bolstered the aerial work platform with lock coils.This new idea shortened aerial work platform installation to one-third what it was before. The engineering industry is now quietly keeping a close eye on whether this fresh technology will become the standard in new methods.
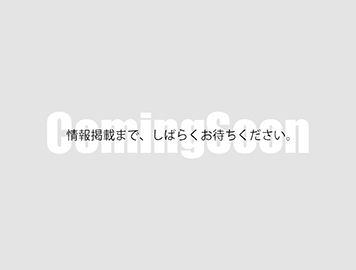
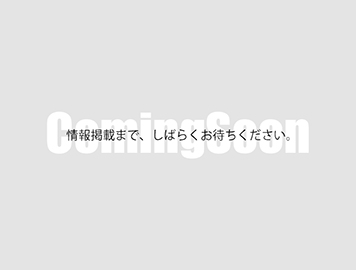
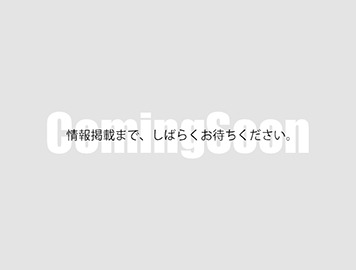
With pride in the technology at the core of Taguchi Industry, we continue to pass that technology on to the future.
Taguchi Industry started out with shaft equipment. Since the company’s founding in the 1950s, we have gained significant trust in this field by refining our technology through dispatching design engineers to Germany, Canada, the U.S., and other Western countries. Our shaft equipment was also used to build the water-sealed underground National LPG Stockpiling Base, a project on the national level to stably supply LPG. Taguchi Industry will continue to nurture the environment and cultivate people to steadily pass on this technology that will certainly be necessary in the near future.
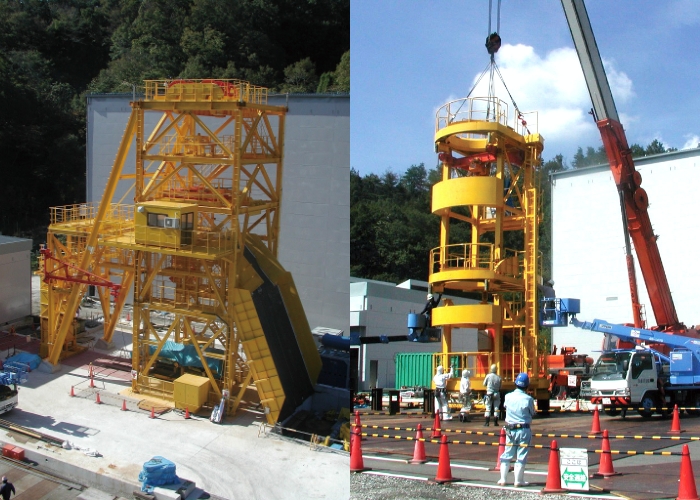
▲Shaft equipment used in the excavation of the Mizunami Underground Research Tunnel
Taguchi’s shaft technology also contributes to research on radioactive waste disposal technology
The cycle of nuclear power generation produces highly radioactive waste.Its treatment requires long-term storage and management in layers more than 300 m deep.To research that, a disposal-technology shaft deep underground was designed.Taguchi Industry’s shaft equipment was adopted for this project to excavate a shaft 500 m underground to investigate underground rocks and ground water.Currently, we are the only company in Japan that has continued to pass on this shaft technology.As the project of radioactive waste treatment moves from the research phase to the implementation phase, the expectations placed on us will be even greater.